FLEXO 101
Tip Tips:
Pondering What Edge to Use – Radius, Beveled or Lamella
Fourth in a 5 Part Series on The Importance of Basic Process Element
The fundamental purpose of the flexographic doctor blade is to remove excess ink from the anilox roll surface. The remaining ink film on the anilox, combined with ink in the anilox cells, needs to be enough to achieve color density on the printed substrate.
If the blade fails to remove enough ink, what remains on the anilox surface transfers more than is necessary to plate and substrate. The excess ink requires more dry time and energy consumption. In addition, the thicker ink film more rapidly overwhelms the plate’s raised image resulting in dot gain, dirty print and mid run press stops to clean the plate.
The converse is not always true. While it is possible to remove too much surface ink from the anilox, especially when metering a low line count surface used in heavy transfer applications, it rarely happens with higher line counts. In fact, flexo made its biggest print quality gains by moving to higher line anilox and all but eliminating the surface ink film. Today’s HD flexo relies on a precise volume of ink from cells, not surface ink films.
The importance of the blade contact area in the metering process can’t be overstated. From the beginning, it was understood that the width of the blade at the point it contacts the anilox surface should be as narrow as possible. The wider the contact
area, the greater the ink’s hydraulic impact. As press speeds increase, hydraulic pressure lifts the blade, allowing more ink to pass and resulting in the list of negatives already mentioned.
CONTACT AREA MANIPULATION
Flexo adopted the use of doctor blades to meter ink from the rotogravure print process. In roto, the blade is used in a wiping position. The dynamics of “wiping” a gravure cylinder, especially in the area that is not engraved, to achieve and maintain optimum performance, are very different than in the sheering or scraping action of the doctor blade in flexo.
The rotogravure press operator purposely manipulates the blade’s contact area to achieve more or less wipe of the area that is not engraved. A very small amount of ink is allowed to pass beneath the blade to lower friction and wear of both the chrome cylinder and the blade. Both the beveled tip and a lamella tip were developed to aid in this process. Part of this manipulation also involves the use of more or less pressure to adjust the blade’s flex.
In the flexo process, the challenge is to set a blade to the anilox at roughly 30 degrees to 35 degrees and keep it there. Most doctor blade metering systems are preset to position the blade at the optimum contact angle. It is much easier to maintain the angle in a single blade system like those common to the label printing industry.
However, chambered blade metering systems are a challenge. Here’s why: During a pressrun, anilox cells trap an increasing amount of air, thereby reducing the amount of ink they hold. To overcome this starvation, the pump’s pressure can be increased to try to force more ink into the cells. Increased pressure within the chamber causes end seals to fail. To stop the end seals from leaking, the chamber and seals are pressed tighter to the anilox. Increased pressure causes blades to flex, bending them over at the tip and increasing the contact area. As the blade tip bends, the contact area widens and the anilox ink film deepens. Dot gain and dirty print soon follow. Chart 1 indicates the contact area at different contact angles when zero flex is present.
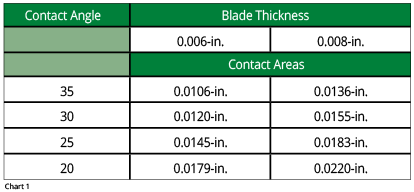
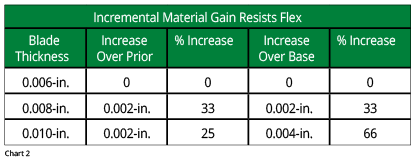
WHEN MORE IS LESS
When it comes to doctor blades, a thicker blade will often result in a narrower contact area. A thicker blade had better resist flexing when pressure is applied. Consider the gain seen in Chart 2 when moving from 0.006-in. thickness to 0.008-in.—that’s 33 percent more material. There are three types of doctor blade tips:
- Radius – For flexo, this is the No. 1 choice. The polished true radius edge is the best performer. It conforms to the anilox radius quickly, with no particular resistance. It is safer to handle and offers a longer run time, as you get a full measure of blade material from the outset. There is also a small price advantage
- Bevel – There are some advantages to using a beveled edged blade in label printing, especially when a single blade holder is used. Elongated bevels with angles less than 10 degrees require no break in time. The beveled edge is easier to see—not always the case at 30 degrees or 15 degrees. The operator should know the bevel must face away from the anilox and should exercise extreme caution when handling. Some wide web printers prefer to use the 2 degree bevel on their new HD flexo applications –
- Lamella – This is the most popular tip for rotogravure printing, because it easily flexes. But remember, flex is a negative in flexo. Lamella seems to be a favorite of press manufacturers. Yet when pressed, their technical staff admit they like the lamella for use in their demo center—where runs are 20 minutes. Otherwise, they would naturally use the radius or beveled tip. Many anilox rolls have been damaged when the lamella bends when pressured to produce large hair like strands of steel
TRUE RADIUS

2 DEGREE BEVEL

15 DEGREE BEVEL

LAMELLA

TO THE POINT
Making the right choice isn’t always obvious. Sometimes a thicker blade achieves a thinner contact area. Using the right blade material, thickness and tip can be critical to the success of a print program. Some blade suppliers offer assistance to help determine which tip and thickness is best for a given application. Anilox roll and ink suppliers also can assist in helping you decide.
If you need help with assessments or training for the best doctor blade solution, contact one of our experts for a consultative evaluation. Our team will be able to help you with solutions.